productivity – a measure of how efficiently a company converts inputs (labour and money) into outputs (products and services)
(Pronounced prod-uk-tiv-ih-tee)
To remember what productivity means use the following mnemonic:
Making these products used to be a labour intensive activity (productivity), but after management measured how the company converts labour and money into products, they replaced the workers with machines.
Productivity in the workplace can also refer to simply how much ‘work’ (products produced, services provided) is done over a certain period of time. Higher productivity correlates with increased efficiency and profits. Levels of productivity can be affected by a range of factors such as training, motivation and the quality of equipment used.
To learn how to improve productivity, senior managers in a business need to understand many up to date production methods, such as:
Just in time manufacturing (JIT) - sometimes called lean manufacturing or lean production. Using small factories, production supplies arrive just before they are needed and finished products are dispatched to the customer immediately. Minimal inventories are kept and mistakes are not allowed to occur. This takes a lot of organisational skills.
Kaizen – this means “continuous improvement” and makes all employees responsible for suggesting ways that the business can continually improve the production process. This is sometimes done every day. Employees gather in teams to talk about the day before and how things could have been done better.
Planned preventative maintenance – instead of waiting for machines to fail and then carrying out repairs, planned preventative maintenance programmes try to prevent a failure by carrying out regular planned downtime to replace parts, oil all the joints and check the condition of each machine.
Flow production – this enables a product to be created in a series of stages on an assembly line. The product moves continuously through the production process. The advantage is that a high number of products can roll off assembly lines at very low cost.
Batch production – if a different product needs different specialisations, it would be best to have an area or cell dedicated to an individual production process. If welding needed doing on one set of products, it would be best to take the product to the cell where the oxyacetylene torches and extraction fans are based. Not all products may need this, but when it does, there is a cell available for the production process. Each cell is a team specialisation.
Amazon is an example of a company that has been very successful is improving its productivity. The company has been able to achieve this by implementing a number of initiatives, including:
- Automating tasks: Amazon has automated many tasks that were previously done manually. This has freed up employees to focus on more value-added tasks.
- Using data to make decisions: Amazon uses data to make decisions about everything from product selection to inventory management. This has helped the company to improve its efficiency and productivity.
- Creating a culture of innovation: By doing this, employees are encouraged and incentivised to come up with new ideas and solutions of how to speed up processes while retaining quality standards.

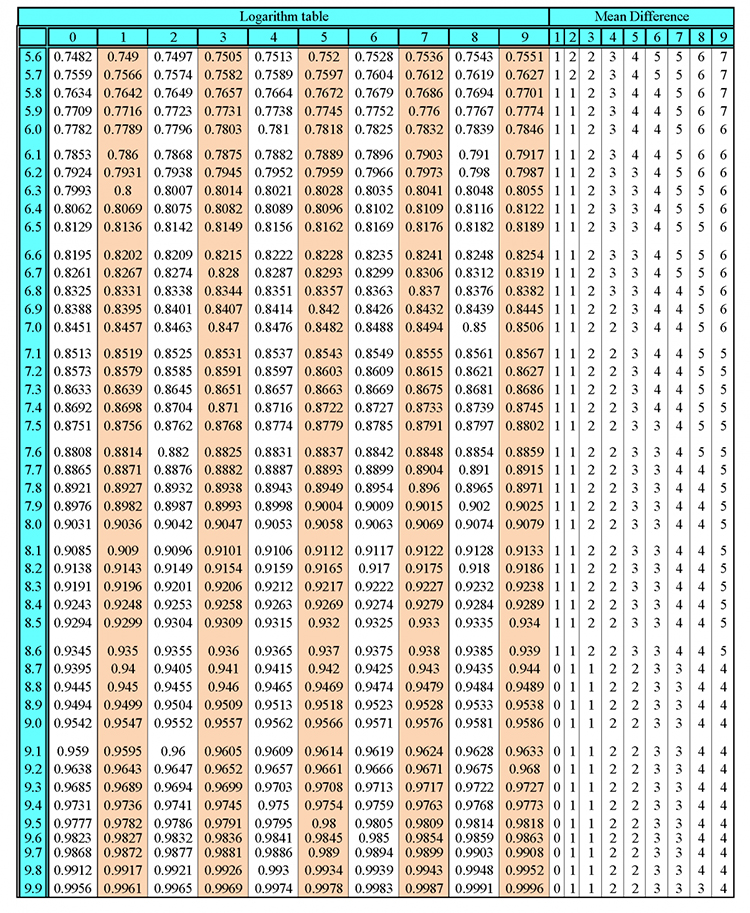
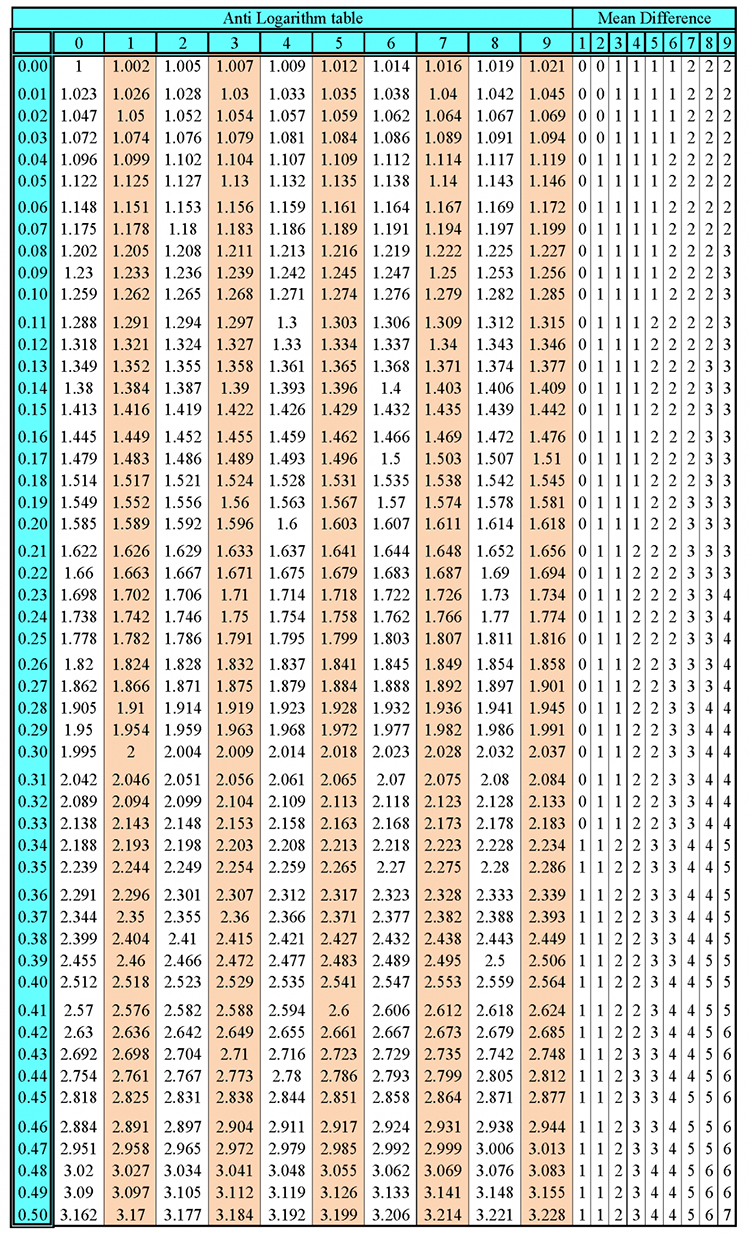
