just in time – an inventory management system in which raw materials and components are delivered just before they are used, reducing the need for storage
Just in time is self explanatory. The system involves receiving materials literally just in time for their use in the production process.
Just in time manufacturing was originally created in Japan and here’s why:
There is so little space on the island of Japan for manufacturing. Any land available was vastly expensive and so any manufacturing had to occur with minimal inventory. No space for stored supplier materials, no space to keep manufactured parts between processes, no space for finished goods and no space for scrap materials.
Japanese manufacturing had to therefore set up a system where supplier goods arrived Just In Time to be worked on. The parts must arrive perfectly (no faults) and in time (no missed delivery times). All machines in the factory must always work, so any maintenance on machines must be planned, ensuring they will not break down between the planned maintenance events (no machine breakdowns). Once the goods are produced and finished in the manufacturing company, they must be delivered immediately to the customer.
Although this is a very difficult system to manage and run smoothly, the manufacturing companies who used the system became, surprisingly to the rest of the world, very profitable world beaters. The rest of the world is trying to catch up and create the same Just In Time system.

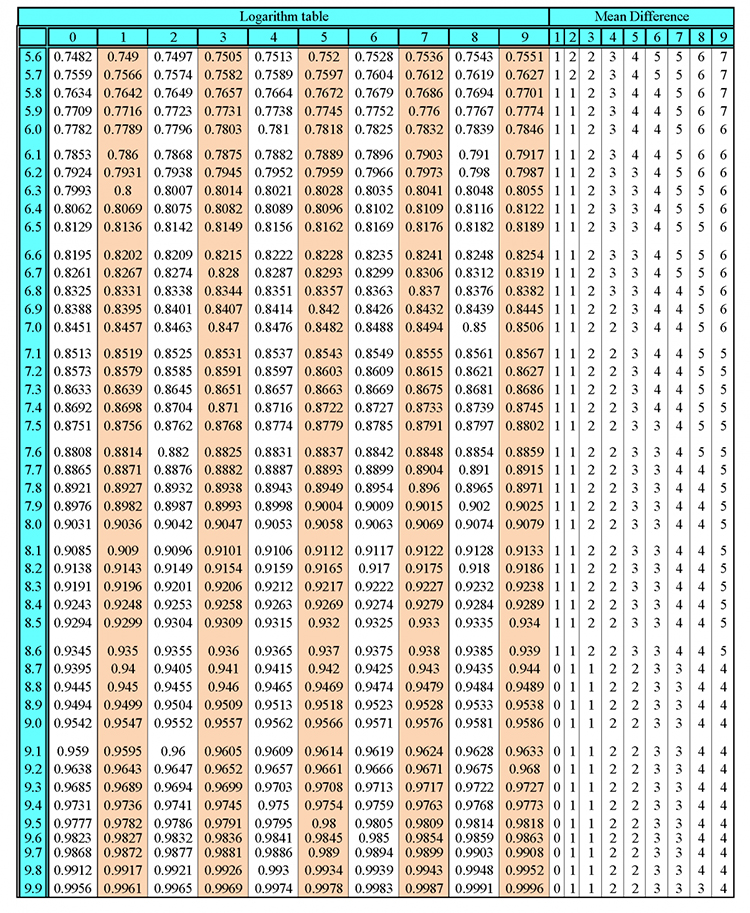
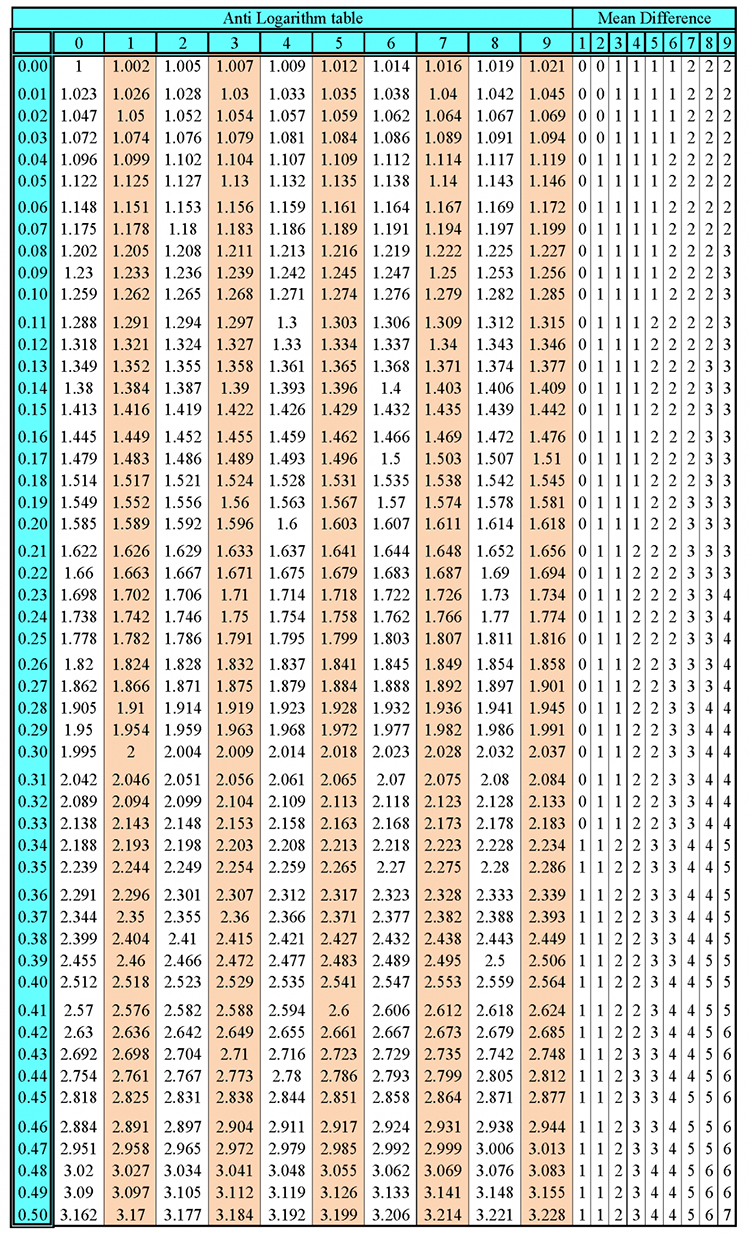
