Unit Cost – The total cost incurred by a company to produce, store and sell a single unit of a particular product manufactured on a large scale
To remember what Unit Cost means use the following mnemonic:
These kitchen units cost (unit cost) very little because they are pumped out by the thousand, but it's easy to work out the costs of one:
Unit cost is calculated by dividing the total cost of production, transportation of raw materials and sale costs (all costs) by the number of units produced:
Unit Cost = Total Cost ÷ Quantity
Note: The total cost is the sum of the variable and fixed costs i.e. all costs.
Variable costs change with the number of units produced such as:
- Shop floor wages
- Raw materials
- Energy costs
- Fuel costs
- Packing costs
Fixed costs are constant (unless there is a step change needed like buying another machine) and include:
- Head office staff wages
- Rent
- Interest on mortgage
- Interest on loans for machines
- Advertising/sales
- Business rates
Here is a very simple example of a company that sells toys by injecting plastic into a mould. 35,000 units can be made in one month. The costs are as follows:
Variable costs
Material cost plastic = £7,000
Shop floor labour cost = £18,000
Energy, fuel and packing cost = £5,000
Total = £37,000
Fixed costs
Head office staff costs = £3,000
Rent, rates, interest = £9,000
Total = £12,000
Unit cost = $\frac{\text{total cost (variable cost + fixed cost)}}{\text{Quantity}}$total cost (variable cost + fixed cost)Quantity
Unit cost = $\frac{£37,000+£12,000}{35,000}$£37,000+£12,00035,000
Unit cost = £1.40 each
Unit cost is then used to work out what price to sell the goods at. If the selling price is the cost to produce plus a margin of say 20%, then the selling price is:
£1.40 + 20% = £1.68 each
An understanding of the unit cost of a product is important for a business. It can then make better decisions about its operations in areas such as pricing, production and profitability.
Note
Once your unit cost is worked out, the same formula is used to work out the marginal cost.
Marginal cost is the change in total production cost that comes from making or producing one additional unit (or ten or even 100 units more).
See the following examples:
Example 1
Let’s take a shoe manufacturing company producing 500 pairs of shoes per month.
Variable costs = £0.75 (plastic and fabric) per pair of shoes
Fixed costs = £1000
Unit cost = $\frac{500\times£0.75+£1000}{500}$500×£0.75+£1000500
Unit cost = £2.75/per pair of shoes
Example 2
Marginal cost to make 1000 pairs of shoes per month
Variable costs = £0.75 (plastic and fabric) per pair of shoes
Fixed cost = £1000
New unit cost = $\frac{500\times£0.75+£1000}{1000}$500×£0.75+£10001000
New unit cost = £1.75 per pair of shoes
The company will see a higher profit margin per pair if all the shoes are sold.
Example 3
Marginal cost to make 1500 pairs of shoes per month.
Variable costs = £0.75 (plastic and fabric) per pair of shoes
Fixed cost = £1000 + £900 cost/month for another machine
New unit cost = $\frac{500\times£0.75+£1000}{1500}$500×£0.75+£10001500
New unit cost = £2.02 per pair of shoes
So now the profit margin per pair has gone down again.
The marginal cost is used to help determine the optimal production levels and price.
It’s important to note that the actual profit made in each example still increases in this case. If each pair of shoes is sold at £3.00 the profit would be:
Example 1
500 pairs of shoes sold in a month
Profit per pair of shoes = £3.00 - £2.75 = £0.25
Profit made is 500 x £0.25 = £125/month
Example 2
1000 pairs of shoes sold in a month
Profit per pair of shoes = £3.00 - £1.75 = £1.25
Profit made is 1000 x £1.25 = £1,250/month
Example 3
1500 pairs of shoes sold in a month
Profit per pair of shoes = £3.00 - £2.02 = £0.98
Profit made is 1500 x £0.98 = £1,470/month

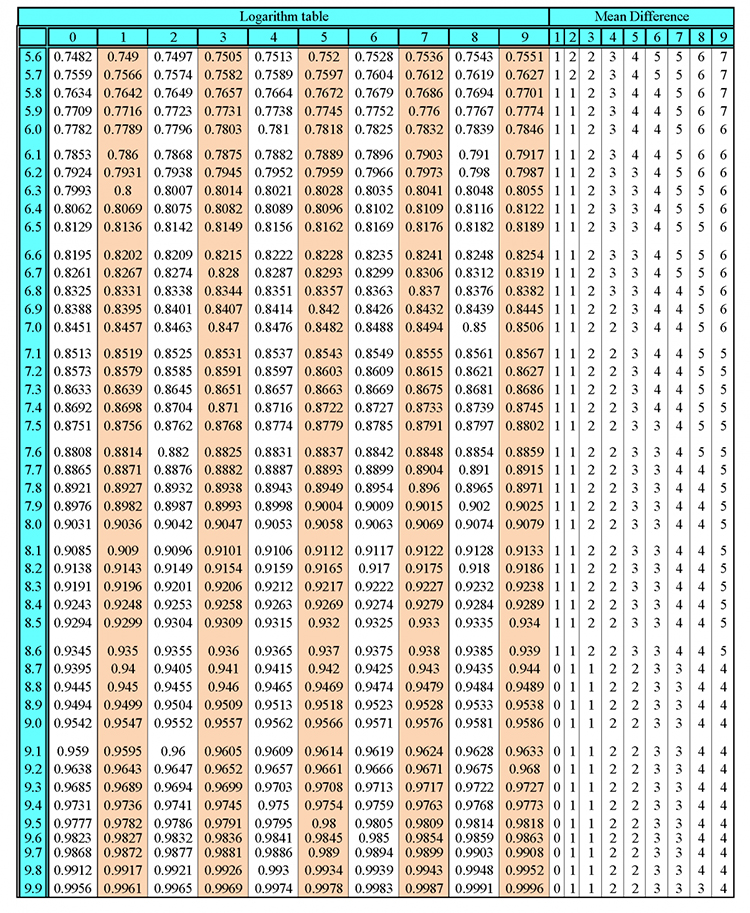
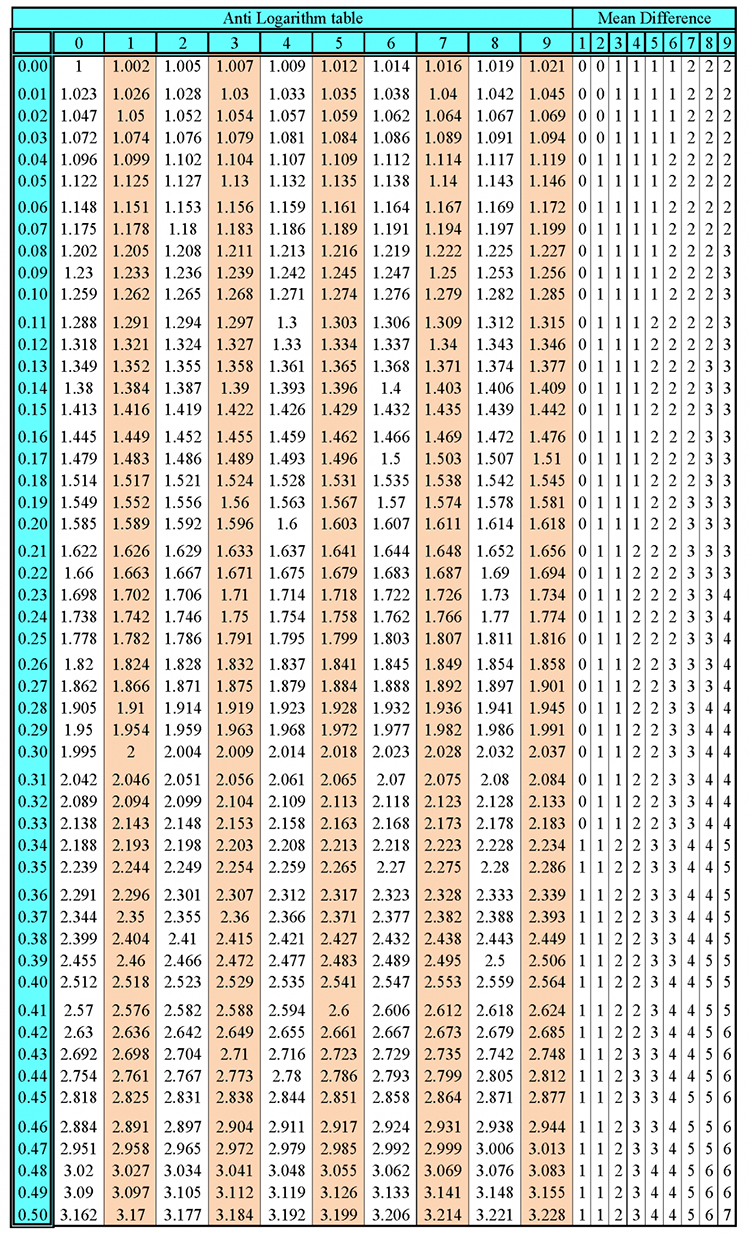
